20ton bow-shaped single-column hydraulic press
20ton bow-shaped single-column hydraulic press
无法加载取货服务可用情况
The bow-shaped single-arm hydraulic press (also known as the C-type single-arm hydraulic press) is a hydraulic equipment with a unique structure, named for its body being in the shape of a "bow" or "C". Compared with the four-column hydraulic press, its most prominent feature is the single-sided open structure. This design gives it a significant advantage in specific scenarios, especially suitable for processing requirements where the workpiece needs to be approached from the side or three sides. The following is a detailed analysis of its core advantages and application scenarios:
I. Advantages in Structural Design
Single-sided open workbench
Three-sided operating space: The machine body is in a C shape (with one side open), and the front, left and right sides of the worktable are completely open, facilitating the operator to clamp the workpiece from multiple directions, adjust the mold or observe the processing process. It is especially suitable for the local processing of large workpieces or irregular parts (such as the press-fitting of long shaft parts and the edge stamping of large plates).
No column obstruction: It eliminates the traditional four-column structure's columns, avoiding the limitation of columns on the operating space. It is suitable for scenarios that require side feeding or processing at special angles (such as single-side punching of automotive parts and bending forming of door frames).
Compact and lightweight single-arm structure
The machine body is rigidly welded as a whole, with a compact structure and a small floor space (usually 1/2 to 2/3 of that of a four-column hydraulic press), making it suitable for small and medium-sized workshops or production environments with limited space.
The single-arm suspension design makes the slider move more flexibly. Combined with the movable worktable, it can quickly switch between workpieces of different sizes.
Ii. Advantages of process adaptability
Suitable for asymmetrical or local processing
The open structure allows one side of the workpiece to be suspended, which is convenient for applying local pressure to long and cantilevered workpieces (such as embossing railway track pads and single-sided flanging of steel structural components).
In processes such as stamping and bending, the edges or corners of the workpiece can be processed directly without the need to place the workpiece completely at the center of the worktable, reducing clamping time.
High-precision guidance and pressure control
It adopts single cylinder drive + linear guide rail guidance (some high-end models are equipped with ball screws or hydrostatic guide rails). Although the structure is simplified, through precision processing and assembly, the straightness and perpendicularity of the slider movement can still be guaranteed (with an accuracy of ±0.05mm), which is suitable for small-batch precision processing with high precision requirements (such as the pressing of instrument parts and the forming of electronic components).
The hydraulic system supports stepless adjustment of pressure and stroke, which can be matched with fine processing of soft materials (such as aluminum and copper) or strong stamping of hard materials (such as stainless steel).
Iii. Advantages in operation and production efficiency
Quick clamping and visual operation
The three-sided open workbench significantly reduces the loading and unloading time of workpieces, making it particularly suitable for flexible production of multiple varieties and small batches (such as mold maintenance and sample trial production).
Operators can directly observe the processing area, adjust the position of the workpiece or the status of the mold in real time, reduce the cost of trial and error, and increase the pass rate of the first piece.
Automated integration is flexible.
It can be easily connected to automated production lines (such as conveyor belts and robotic arms), and achieve full-process automation through side or front feeding (for example, in the production line of automotive seat frames, robots are used to pick up workpieces from the side to complete press-fitting).
Some models are equipped with rotary worktables or adjustable Angle fixtures, expanding the multi-angle processing capabilities.
Iv. Maintenance and Cost Advantages
Low maintenance cost
The structure is simple, with a small number of hydraulic components (usually only one main cylinder + base valve group), few oil leakage points, and low daily maintenance workload.
The guiding system adopts maintenance-free guide rails or centralized lubrication design to reduce the frequency of manual maintenance.
Outstanding cost performance
The manufacturing cost is 10% to 30% lower than that of the four-column hydraulic press of the same tonnage, making it suitable for small and medium-sized enterprises or individual processing households with limited budgets.
Energy consumption optimization design (such as rapid downflow without load and slow pressurization under load) reduces power consumption and is more economical for long-term use.
V. Typical Application Scenarios
Automobile parts processing
Door hinge press-fitting, shock absorber piston rod straightening, exhaust pipe elbow forming.
Metal products industry
Kitchenware (such as rolled edges of cookware), perforated Angle steel of shelves, and bent hardware for doors and Windows.
The field of electronics and home appliances
Motor stator press-fitting, compressor component forming, and local stamping of home appliance panels.
Mold and tooling maintenance
Local finishing of mold parts, clamping test of small molds, and clamping of fixtures.
Special industry
Processing of small structural components in the aerospace field (such as pressing aluminum alloy brackets), and forming of precision parts for medical devices.
Share
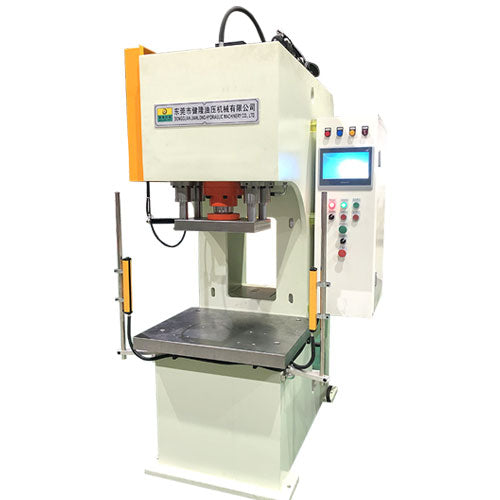
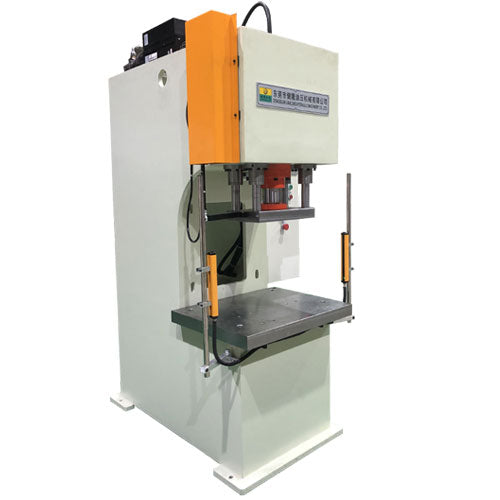
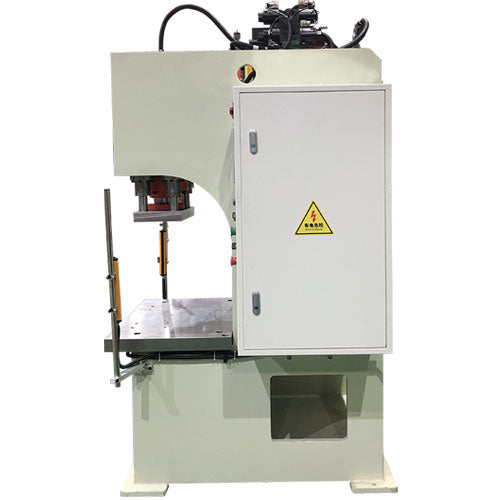
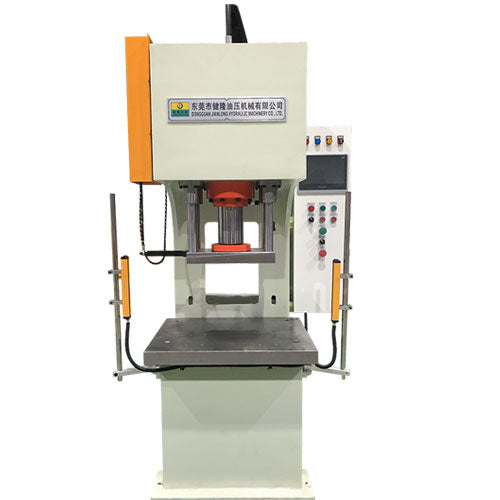
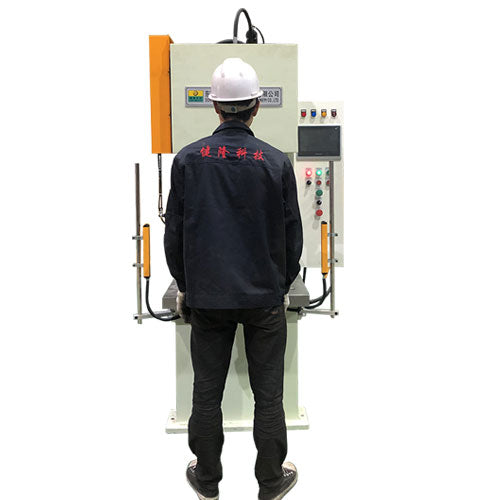